El objetivo del proyecto es la implantación de un modelo lean manufacturing en la sección de TELARES a través del análisis de la cadena de valor (VSM), así como el pilotaje y desarrollo de las acciones de mejora que emanen del mismo.
Se pretende analizar el proceso desde el punto de vista de la creación de valor (VSM) identificando aquellos puntos susceptibles de mejora, y ante todo un plan de acción concreto y detallado que pueda llevarse a cabo por un equipo interdisciplinar, pilotado por QE2 eConsulting.
La herramienta de las 5S ha supuesto un cambio muy visible, que ha arrastrado a su vez al equipo a desarrollar acciones en otros ámbitos de la planta.
BLOQUE A: CAPACIDAD
- Estudio de capacidad productiva de la sección telares por familias de referencias.
- Modelizado de proceso (diagrama QQ).
- Auditoría de proceso FIEV.
El primer paso requirió realizar el modelizado de los diferentes procesos. Esto nos permitió definir indicadores para poder establecer metas y objetivos, detectando de forma científica los puntos de mejora (mudas, restricciones y cuellos de botella).
En esta fase se abordó la definición de puestos / funciones a través del diagrama QQ (o diagrama swimlane), así como la realización de un estudio de capacidad productiva por familias de referencias.
BLOQUE B: VSM ESTADO ACTUAL
- VSM del estado actual por familias/ grupos de referencias.
- Mejora de la productividad.
- Organización y planificación de la producción.
- Imbricación de la producción con procesos complementarios.
- Dimensionamiento de recursos humanos y materiales.
- Enfoque ISO.
Tras la fase inicial de estudio de capacidad y modelado, se comenzó con el VSM del estado actual, para lo cual se tomó un enfoque coherente con la fase anterior: cada grupo o familia de referencias tuvo un VSM individual, de forma que la información fue más ajustada a la realidad. Además del estado actual, se realizó una propuesta del VSM futuro, donde se mostraron las diferentes acciones necesarias para su consecución.
BLOQUE C: PLAN DE ACCIÓN + MEJORA CONTINUA
La realización del VSM se compone del VSM del estado actual y el VSM del estado futuro. Para evolucionar del primero al segundo, es imprescindible un plan de acción concreto y obtenido a partir del conocimiento de la propia empresa: la mejora está en uno mismo.
- Determinación de responsables/ plazos para cada acción.
- Pilotaje y monitorización de las diferentes acciones.
- Asesoría y colaboración en los diferentes proyectos llevados a cabo: soluciones tecnológicas, contacto con proveedores especializados, etc.
- Creación de objetivos de producción, seguimiento y monitorización Creación de equipos de trabajo, buscando el aporte de soluciones de diferentes ámbitos de la empresa: se busca la participación de todos, lo que mejora la motivación y aporta valor a los proyectos.
- Imbricación de los proyectos de mejora en el sistema de reuniones frecuenciales de seguimiento.
- Creación de un sistema de seguimiento de no conformidades.
El modelo productivo culmina con la implantación de la mejora continua, que se materializa a través de los siguientes ítems:
- Optimización de todos los recursos existentes, integrándolos en el sistema de gestión.
- Formación e información al personal, tanto del sistema creado como de herramientas concretas de mejora.
- Creación de grupos de mejora.
- Creación de sistema de reuniones frecuenciales (semanal, mensual, anual) para el seguimiento de cumplimiento de objetivos de producción, análisis de indicadores e introducción de proyectos de mejora.
- Implantación de la metodología de análisis de causas y resolución de problemas, como respuesta al sistema de seguimiento de no conformidades.
- Implantación de diversas herramientas de gestión productiva: 5S, KAIZEN, KANBAN.
BLOQUE D: VSM ALCANZADO
Tras la fase de desarrollo de acciones, se conecciona el VSM del estado futuro alcanzado. Asimismo, se deajn plasmadas las acciones a medio y largo plazo necesarias para la evolución a un estado futuro mejorado:
- VSM del estado futuro.
- Enunciado de acciones a medio/ largo plazo
LOGROS CONSEGUIDOS
Durante el año que ha durado el proyecto, se ha conseguido dar un giro a la sección TELARES, tanto en imagen de planta como en modelo de gestión.
La herramienta de las 5S ha supuesto un cambio muy visible, que ha arrastrado a su vez al equipo a desarrollar acciones en otros ámbitos de la planta.
Entre las diferentes mejoras, podemos destacar las siguientes:
- IMAGEN DE PLANTA: si bien conviene destacar que el punto de partida ha sido ya de por sí positivo (ya desde un principio la planta se encontraba limpia y ordenada), es cierto que el cambio ha sido notable. A través de las 5S se ha logrado imponer un sistema de factoría visual, en el que las ubicaciones de los diferentes elementos son obvias y están debidamente señalizadas. Esto ha redundado en una mayor productividad, al reducir tiempos y mejorar la seguridad, entre otros aspectos.
- DOCUMENTACIÓN EN PLANTA: uno de los puntos más interesantes ha sido la mejora introducida a través de las FIRM (Ficha de Instrucción de Reglaje de Máquina), que garantiza que los parámetros de máquina estén debidamente controlados y registrados, impidiendo cambios subjetivos no sujetos a trazabilidad. Un producto como el de MESA requiere de un control de proceso que asegure su calidad, por lo que los parámetros de máquina son un aspecto crucial.
- FLUJO DE TRABAJO: se ha implantado un Kanban entre retorcido y telares, que regula el flujo de material, lo que reduce los stocks y por tanto, aumenta el aporte de valor, tal y como se puede comprobar en el VSM realizado como vehículo vertebrador del proyecto.
- CAPACIDAD PRODUCTIVA: uno de los puntos más interesantes del proyecto, es la realización de una herramienta informática para el cálculo de la capacidad productiva de la sección, lo que permite planificar la producción de una forma mucho más exacta, reduciendo los costes al aprovechar los recursos de una forma mucho más eficiente.
- FLUJO DE INFORMACIÓN: en toda organización, el flujo de información suele ser foco de diferentes problemas cuando existen barreas que impiden la conexión entre emisor y receptor. El método más efectivo es la creación de un sistema de mejora continua, que, a través de indicadores y reuniones frecuenciales, garantice que la información llegue a su destino, debidamente cuantificada y verificada. Esto es precisamente lo que se ha sembrado a lo largo del año de proyecto.
LA HERRAMIENTA
Por sus siglas en inglés “Value Stream Mapping” o “Mapeo de la Cadena de Valor”, es un diagrama de flujo especial que utiliza el “lenguaje LEAN” para describir y mejorar el flujo de materiales y de información, identificando claramente dónde se aporta valor.
Si entendemos como valor aquello que nuestro cliente aprecia en mayor medida, nuestro producto o servicio deberá maximizarlo. El proceso de hallar este valor incluirá una investigación del carácter de nuestro cliente. Una vez hallado debemos ubicar esas expectativas del cliente dentro de nuestro propio proceso. Ahí entra la definición del flujo de valor y su optimización.
El objetivo es proporcionar el óptimo valor al cliente a través de un proceso de creación de valor con el mínimo desperdicio. ¿Cómo? en tres facetas:
- Desde el Diseño orientado al cliente.
- Fabricación, de la recepción del pedido hasta la expedición.
- Mantenimiento, en el periodo de uso de ese producto o servicio. Atención al cliente.
¿Por qué es importante el VSM? Muchas organizaciones persiguen la conversión a Lean pero han realizado mejoras aisladas que no son suficientes (eventos de mejora crean mejoras localizadas). VSM y su análisis fortalecen las ganancias proveyendo de una visión y planificación conectando todas las actividades de mejora. Es decir, VSM y su análisis es una herramienta que permite ver el desperdicio y planificar cómo eliminarlo.
En definitiva:
- Mejoramos la eficiencia del sistema LEAN
- Conectamos las mejoras de una manera interdisciplinar.
- Reducimos el desperdicio, reducimos los costes.
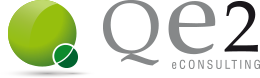